生产过程可追溯管理的5大核心优势:实时记录业务行为提升制造业竞争力
在制造业中,生产过程可追溯管理已从“加分项”演变为“生存刚需”。无论是应对突发质量问题,还是优化供应链效率,企业都需要依赖实时记录技术,将原材料、生产工序、质检结果等全链路数据精准留存。传统依赖手工录入的纸质台账,不仅存在数据滞后、人为误差等风险,更可能因追溯链条断裂导致召回成本激增。据行业统计,采用智能化追溯系统的企业,质量问题处理效率提升67%,客户投诉率下降42%。
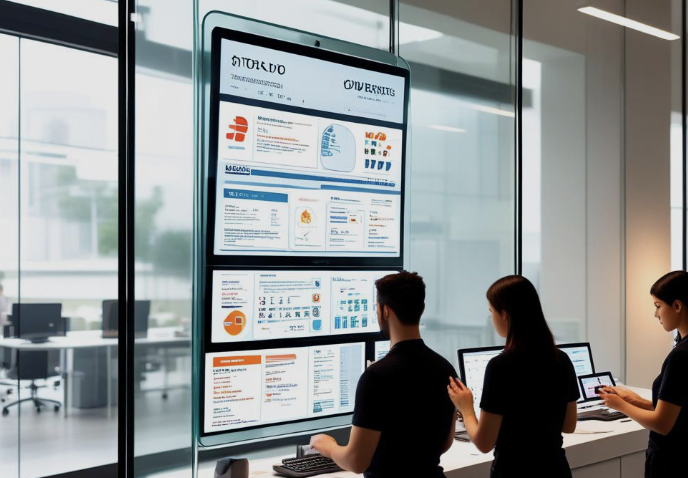
一、可追溯管理的战略价值:从风险规避到品牌增值
生产过程可追溯的核心在于构建“数据闭环”——从原料入库到成品出库的每个节点,均需记录业务行为的完整轨迹。例如,某汽车零部件企业通过引入物联网传感器,实现了冲压工艺参数的毫秒级采集,当检测到某批次产品厚度偏差时,系统可在10分钟内定位到具体机床的模具磨损问题,避免近千万元的经济损失。
这种能力直接关联企业的两大核心诉求:
风险控制:通过批次管理(Batch Management)锁定问题范围,避免大规模召回。如制药行业通过一物一码系统,可将受影响药品的追溯时间从48小时缩短至5分钟。
合规竞争力:欧盟《CSRD可持续发展报告指令》等法规要求企业披露生产环节的碳排放、原材料溯源等信息,可追溯数据成为国际市场准入的“隐形门槛”。
二、实时记录技术的3层革新:从手工录入到智能决策
传统手工录入的弊端显而易见:某食品企业曾因员工漏填灭菌温度数据,导致整批产品被判定为“过程失控”,被迫销毁。而智能化系统通过以下架构实现突破:
数据采集层:RFID标签、工业相机等设备自动捕获生产行为,取代人工抄录,确保数据准确性提升至99.8%以上。
分析层:通过机器学习模型识别异常模式。例如,当注塑机的压力曲线偏离历史基准时,系统自动触发预警,早于传统质检环节48小时发现潜在缺陷。
应用层:数据反向指导工艺优化。某新能源电池企业通过分析正极材料涂布工序的实时数据,将良品率从89%提升至96%。
引瓴数智的生产过程可追溯管理系统(www.yinlingshuzhi.com)正是这一技术的典型代表,其区块链存证功能可确保数据不可篡改,特别适用于医疗器械、航空航天等高风险行业。
三、可追溯系统的ROI测算:看得见的成本,看不见的收益
企业决策者常质疑:投入数百万元部署系统是否值得?事实上,隐性收益远超硬件成本:
质量成本降低:提前发现问题的成本仅为事后处理的1/10。
供应链协同增效:当上游供应商的原料批次数据与生产计划实时同步时,库存周转率可提升30%。
品牌溢价创造:某婴童用品企业通过官网公示“生产溯源地图”,客单价提升18%,消费者复购率增加25%。
行动指南:4步实现可追溯管理升级
诊断业务痛点:优先在质量事故高发环节(如焊接、装配工序)部署数据采集点。
选择适配技术:离散制造企业可侧重MES系统集成,流程行业则需强化批次追踪能力。
建立数据治理标准:定义关键参数的采集频率、精度要求和存储周期。
培训与迭代:通过模拟故障演练,让质量控制专员掌握数据溯源技巧。
<本文由引瓴数智原创,商业转载请联系作者获得授权,非商业转载请标明:引瓴数智原创>
作者:引瓴数智
【引瓴数智www.yinlingshuzhi.com】是一家专注于为企业提供一物一码平台全链数字化运营方案服务提供商,一物一码管理系统一体化全方位的行业数字化转型解决方案,对企业进行全渠道覆盖,供应链管理整合,精细化运营,大数据挖掘。
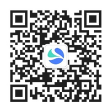
全部评论